トヨタ式カイゼンの目的とは? 事例から学ぶ改善手法
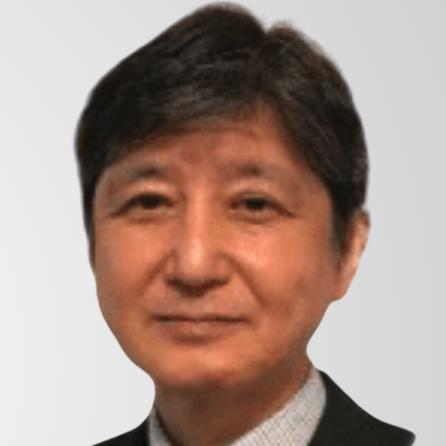
池谷 卓
中小企業診断士
約30年以上にわたり、素材メーカーに勤務し、国内外の生産設備・ライン
設計・保全や生産拠点運営、新事業開拓、経営企画、DX推進等を経験。2023年に中小企業診断士として登録。
\認定支援機関!補助金のプロの中小企業診断士がサポート/
カイゼンの意味とは
カイゼンは、欧米企業に見られるような「トップダウン的・幹部主導型」の作業改善に対して、多くの日本企業が進めていた「ボトムアップ的・現場参加型」の作業改善活動です。
では、カイゼンの意味はと聞かれて、なぜ「改善」ではなくて「カイゼン」なのかを的確に説明できますでしょうか?
両者は日本語としては読みも意味も同じですが、これらには明確な違いがあります。
- 改善
一般的に「悪いところを改めてよくする」ことを意味します。また、JIS Z8141-2022では、「生産システム全体、またはその部分を見直し、能力その他の諸量の向上を図る活動」となっております。英語では「IMPROVEMENT」に相当するとしています。 - カイゼン
現状に満足せずに、常にさらに良い状態へ変化し続けるとの意味合いが含まれています。つまり、「継続的に改善を行う事」がカイゼンということになります。「改善」という言葉は、似た言葉の「改良」と比べて抽象的な概念をあらわす言葉です。そして、「カイゼン」はさらに抽象度が高くて「普遍的に、現状で満足せず、より良い状態を目指して改善を継続、繰り返していく活動」を指す、哲学的な要素を含んだ言葉なのです。この点を少し拡張すると、仕事とは「作業や業務だけでなく、同時にカイゼンを行うこと」ということができます。 - KAIZENカイゼンは、「CONTINUOUS IMPROVEMENT」と訳される場合が多いですが、それですと先に示したカイゼンの意味合いを完全に表現することができないため、海外では「KAIZEN」という言葉が広く使われているようです。
「カイゼン」や「KAIZEN」は海外を中心に、現在では建設業、サービス業、医療、小売業など幅広い分野で活用されています。また、米国を中心に海外で研究が進んでおり、将来的には、新たな「カイゼン」の考え方が生み出されて、米国などから逆輸入される時が来るかもしれません。
\認定支援機関!補助金のプロの中小企業診断士がサポート/
トヨタ式カイゼン活動
カイゼンの意味とは
トヨタにとって、改善を続けることは経営の根幹になっています。2020年に発表された、トヨタ社員の最新の行動指針である「トヨタウエイ2020」中にも以下の記載があります。
- どんな小さな仕事でもつねに進化を求め、今日までのあり方に満足しない。
- どんな小さな改善も明日のイノベーションに通じている。
これら記載された文章は、先の行動指針である「トヨタウエイ2001」の、改善、革新の追求の流れを受け、「カイゼン」の考え方を土台にしていると考えられます。
トヨタ式カイゼンは、戦後まもなく、大野耐一がトヨタ生産方式の出発点として考えた「日本人がやっている大きなムダ」を徹底的に削減・排除することに根差しています。そのために、「あるべき姿」を設定して、それを達成するために「カイゼン」を行います。「あるべき姿」が達成できれば、さらに上の「あるべき姿」を目指すといったように、組織自身の進化していくサイクルを生み出すことができ、トヨタ式カイゼンでは3つのレベルの「あるべき姿」を設定しています。レベル1は“標準がある姿”、レベル2は“標準通りにできる状態”、そしてレベル3は“常に標準が進化している状態”になります。
- レベル1
生産現場のあるべき姿としての作業手順、サイクルタイムや標準の手待ちなどが標準として設定されていて、作業者が目標と現状の違いをはっきり認識できる状態です。 - レベル2
標準の目標通りの作業を行うことができるようになっている状態です。しかし、この現状に甘んじていては「改善を続ける」ことにはなりません。 - レベル3
あるべき姿をさらに高めて設定して、新たな目標設定を行います。
トヨタ式カイゼンでは自分たちがどのレベルにいるのかを把握して、現場での落とし込みをスムーズにして、周知・徹底を行うことから始まるのです。そして、このようなステップで継続的に改善を進めていくことで、組織は常に進化し続けることができます。
このような活動は、トヨタ生産方式の柱である「広義の自働化のコンセプト」を体現しているといえます。
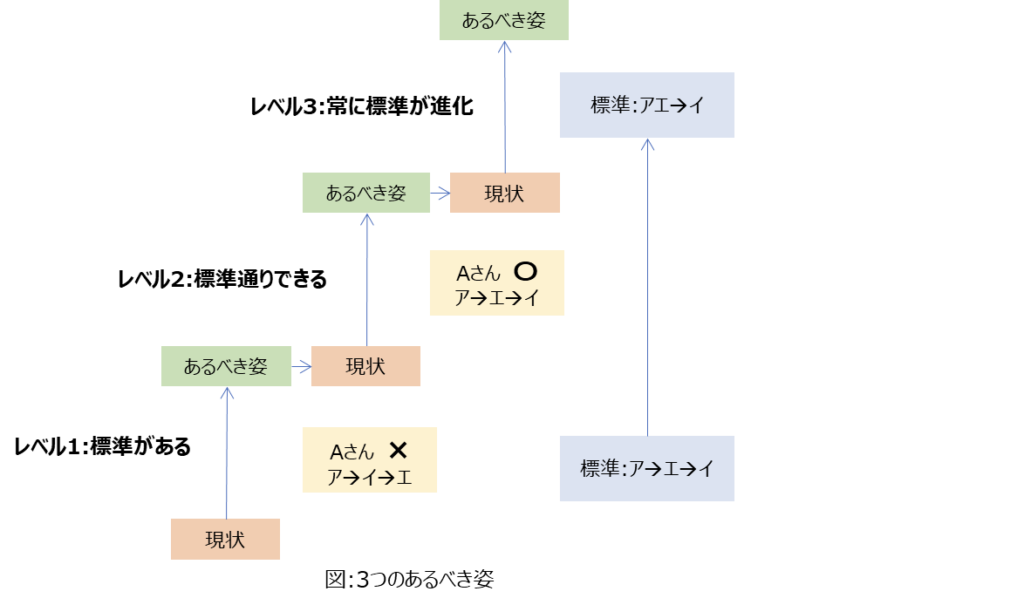
次に、トヨタ式カイゼンは一般的な生産現場と同じでチームを組んで作業を行っています。そこで生産性の向上を図るためには、チームや組織に所属している作業員のチームワークの良くすることが大事になります。例えば、野球でも、1~2人のスター選手がホームランを何本も打つことができても、チームワークが良くないとゲームに勝てないことと似ています。
しかし、選手同士だけに任せておけばよいかといえばそうではありません、選手同士だけでなく、監督やフロントとの良好なコミュンケーションや、チームとしての共通の目標を設定することにより、選手のモチベーションは高くなりチームワークも良くなって、最終的な目標である勝利を勝ち取ることができるのです。
トヨタ式カイゼンにおいても、同様に経営層と従業員同士のコミュニケーションを重視しています。経営者は現場で起こっている問題点を理解し、企業としての目標を従業員にしっかり伝えることが大事です。従業員側からも経営者側に対して、現場での問題点、改善案などを自由闊達に言うことができる環境作りが必要だということです。
トヨタ式カイゼンの目的は生産性向上ではなく、誰かの仕事を楽にすることです。誰かの仕事を楽にした結果として、生産性が向上すると考えています。つまり、トヨタ式カイゼンには、働いている人を中心としたカイゼンフィロソフィーがあるということになります。
3Mを最小限に抑える方法
3Mとは、現場における「ムリ」、「ムダ」、「ムラ」のことです。
「ムリ」とは、ある工程や作業、または作業員に能力以上の負荷がかかっている状態を指します。この状態を継続していると、一時的には成果が出ていても必ず綻びが生じて、場合によっては設備故障、作業員の精神的、または肉体的な安全を守れないだけなく、社会的な災害を発生させる原因にもなります。
「ムダ」とは、付加価値を生まない非効率な作業のことを指します。探し物をする、時間と手間がかかるなど生産性が低い作業のことです。先にも述べた通り、トヨタ生産方式の出発点となっていますが、トヨタ式カイゼンでも非常に重要です。
「ムラ」とは、業務にばらつきが生じていることを指します。それにより、人員配置や生産計画に問題が発生し、作業時間や製品品質に影響を及ぼす可能性があります。
このような3Mの削減は生産性向上に直結していることから、トヨタ式カイゼンにおいて特に力を入れて取り組んでいる活動です。「ムリ」、「ムダ」、「ムラ」を削除できれば、生産性向上、コスト削減や品質安定などだけでなく、作業負荷の低減を実現できることになります。
5Sを重視する理由
5Sは職場環境をよくするための言葉の頭文字をとったもので、以下にそれぞれの言葉とその意味を示します。ちなみに5Sという言葉は、先のKAIZENと同様、そのまま海外で通用するほどに有名です。
5Sを進めることによりムダな動きや時間のロスを削減し、作業の流れをスムーズにできます。
・ 整理(Seiri) 不要なものをすてること
・ 整頓(Seiton) 使いやすいように整理すること
・ 清掃(Seisou) 掃除をすること
・ 清潔(Seiketsu) きれいな状態を維持すること
・ しつけ(Shitsuke) 習慣化するようにルール化すること
例えば、整理、整頓が進んでいない現場ですと、ほしい部品や道具を探すのに時間がかかってしまい、ムダな作業が発生してしまいます。まずは不要なものを捨て(整理)、使いやすいように整理し(整頓)、掃除をして(清掃)、きれいな状態を維持する(清潔)ことが重要です。それにより、ムダ時間などを削減できることに加え、労働安全や設備故障を予防することができます。
5Sが徹底された現場では、作業員の方や管理者の方のコミュニケーションが密になるため、作業員と管理者のカイゼンに対する価値観や目線が統一され、自然とチームワークがよくなります。
カイゼンの進め方と手順
効果的なカイゼンを目指すためには、以下の手順で進めていく必要があります。特に、組織文化としてカイゼンが定着していない場合には、管理者の「カイゼンを進めていくのだ」という強い思いが必要になります。
課題を洗い出して、明確にする
改善のアイデアを出す、出し合う
改善のアイデアを実行する
実行しながら結果を評価し修正する
問題や課題を特定する方法
課題の良し悪しがカイゼンの方向性や最終的な質に大きく影響を与える可能性がありますので、このステップは非常に重要です。
良い課題とは「難しい課題」であると考えて設定しようとする方がいますが、大半はカイゼン効果を得ることができないためお勧めしません。逆に現状で困っているような問題や課題はないとおっしゃる方もいますが、これも間違いです。
現場や作業工程のあるべき姿を管理者と現場作業員でコミュニケーションをとりながら決めて、そのあるべき姿と現状の差異を埋めるために、解決しなくてはならない課題を設定してみると良いかと思います。良い課題が設定できるということは、カイゼンのメリットをしっかりイメージできているということなので、チームとしてモチベーション高くカイゼン活動に取り組むことができます。
改善アイデアを具体化する方法
課題を設定できたら、次には具体的な改善アイデアを考えます。課題設定と同じように実行が難しいものや時間がかかるアイデアではなく、効果的ですぐに実行できるアイデアを選択することがポイントになります。早めに成果が出るので、チームメンバーのモチベーションを高める事ができ、継続的な改善活動が可能になります。
アイデアを出す際には、チームメンバーと親和図法などを使ってブレインストーミングで自由に意見交換して、新しい考え方や組み合わせ、視点などを取り込むようにすると良いと思います。
実行中の評価とフィードバック
固まったアイデアを基にして、チームメンバーと一緒になってカイゼン活動を実行しましょう。途中で実行の結果やそのプロセスを定量的、定性的に評価することが重要です。
定量的な評価では、ヒストグラム、パレート図、管理図や散布図などQC7つ道具などを活用すると見える化ができ、チームメンバーや関係者とも共通認識が図れます。そのことにより、あるべき姿とのギャップや新たなあるべき姿の設定、アイデアの方向性変更など、カイゼンのPDCAを確実に回すことができるようになります。
\認定支援機関!補助金のプロの中小企業診断士がサポート/
製造業におけるカイゼンの具体例3つ
ここでは、カイゼンの具体的な事例をいくつかご紹介します。
1. 作業工程の可視化方法
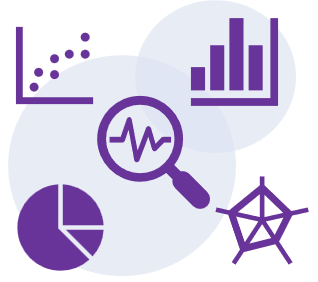
製造業において、生産工程や生産設備の状態を見える化することは非常に大事なことです。見える化をすることによって、現場の状態が正常か異常かを客観的に判断でき、正常にするために管理することができます。これはトヨタ生産方式でいう「目で見る管理」に相当します。
トヨタ生産方式の場合、現場の見える化として、現場に設置されているアンドンで生産ラインの正常、異常が一目でわかるようになっており、物の置き場の見える化もなされています。また、作業の見える化に関しては、作業員のスキルの見える化による多能工化が進められています。さらにデジタル技術などを活用した生産工程や生産設備の状況把握、在庫管理など、スマートファクトリーの取り組みが行われています。
当該社は、オイルシール金型を製造・販売を手掛ける会社です。
当該社では、まず社長以下各部署からプロジェクトメンバーを募り、自社の強みや事業環境を分析して、特に生産面において強化すべき課題と、そのために必要な対策の検討を行いました。優先順位の高い対策として、生産設備の負荷状況や稼働状況を見える化をすることで、柔軟性の高い生産計画立案を目指すこととしました。システム導入に先立ち、システム導入後の業務のあるべき姿も明確にしてから見える化を実施した結果、加工時間を従来よりも2/3まで短縮して、競合他社では実現不可能と思われる低コスト、短納期を実現することができました。見える化で一番大事なことは、状態・状況を共有できるということではなく、その情報を基にカイゼンを実施するということです。単に状態・状況を見せているだけの生産現場もありますが、そうならないように特に管理者の方は注意が必要です。
2. 標準化された業務のシステム化
製造業においては、顧客情報管理や棚卸在庫管理、図面管理など定型業務が沢山存在しています。そしてその多くは、かかる労力と時間の割には生み出す付加価値が少ない作業です。そのため、これら定型業務をシステム化によって自動化・省力化することは、付加価値生産性を高めることに直結します。
しかし、やみくもにシステム化に取り組むことはお勧めしません。まず、「どれくらい定常作業があって、どれだけ労力や時間がかかっているのか?」、「それらの定型業務は、現在のビジネスにおいて本当に必要なのか?」、「もし必要であれば、システム化を進める前にカイゼンできることはないのか?」、「それら定常作業のあるべき姿とは、どのようなものか?」との問いかけをしてみてください。
すると、システム化の前にやるべきことが明らかになり、システム化導入後のあるべき姿までイメージすることができます。中には、このようなプロセスは大変だから、ITエンジニアに任せればよいと考える方がいますが、それは絶対にやらないでください。
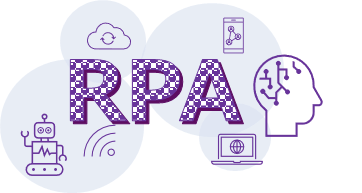
当該社は、産業機械部品等の銅製品の製造・販売を手掛ける会社です。
当該社ではシステム化に当たり、社長以下各部署からのプロジェクトメンバーがRPA導入教育を受講しました。
まず、プロジェクトメンバーで受注業務の各工程の関係など全体像を明確化にした後、あるべき姿を明確にして、不要な工程をやめて他の工程と一緒にするなど、必要によっては顧客をも巻き込んだカイゼンを行い、工程数を1/4に減らしました。その後、RPA導入を実施した結果、受注業務時間の75%を削減することに成功することができました。
3. 追加のツールによる作業時間の短縮
製造業の場合、治具、道具を使ったり、既存設備の動力、重力や機構などを使うことによって作業時間を短縮したり、作業員の負荷を低減することができます。追加ツールの導入によるカイゼンの場合は、現状肯定をせずに問題点があるのだとの態度で臨むことが一番必要です。
\認定支援機関!補助金のプロの中小企業診断士がサポート/
カイゼンの進化と現代の価値
QCサークル活動の進め方|成功させる4つの基本要素とポイント
皆さんご存じのデミング博士が日本に招待され、品質管理セミナー(※)を開催したのをきっかけに、その後日本独自の品質管理手法が開発・浸透し、1975年に頃には現場中心の品質管理から全社的な品質管理(TQC)へと発展しました。
※本セミナーでPDCAサイクル(デミングサークル)が提唱されています。
TQCは、「経営層による方針設定」という「トップダウン」的な活動が重視されている面もありますが、その中で、QCサークルは「同じ職場内で品質管理活動を自主的に行う小グループ」として、継続的な品質管理や品質改善活動に取り組む「ボトムアップ」的活動として定着しました。
QC活動では「自主的にチームメンバーが能力開発をしながら、チームでの継続的なカイゼン活動を通じて顧客満足度の向上を行うことにより、経済的・社会的な価値の創造を実現する」ことを目指します。
「人・メンバー」の要素
QC活動の最小参加単位である「人・メンバー」は、一般的なチーム・組織活動と同様、それぞれのメンバーの能力よりもメンバーのモチベーションのレベルが重要です。個々人の努力だけに頼るのではなくて以下のようなことを考え、モチベーション向上を図ることをお勧めします。
・ メンバー同士のコミュニケーションをよくするための機会を設定する
・ メンバーが学習する機会を積極的に提供する
・ 部門、または全社的な活動報告会を行い、各活動成果を表彰・承認する
・ 社外活動・イベントなどへの参加の機会を提供する
「チーム」の要素
チーム・組織活動を活発にするためには、そこに参加しているメンバーがある程度同じ価値観を持って、自主的に活動をする必要があります。そのために、それぞれのメンバーが別々に活動するのではなく、積極的に協同して活動する必要があります。それによりメンバー間のチーム・組織に対する認識が揃うだけでなく、組織学習の面において効果を発揮することができます。トヨタ生産方式においても「離れ小島を作るな」と言われているように、個々人だけで作業をすることはチームワークを発揮する邪魔になると考えられます。
「カイゼン活動」の要素
QCサークルでカイゼン活動を進めるためには、適切なカイゼン活動目的や目標、さらにはテーマを設定することが重要です。チーム活動を活性化するために非常に高い目標を掲げる方がいますが、それは推奨できません。もちろん低くて簡単に達成できる目標は意味がありませんが、少し努力することによって到達できる程の目標を設定することをお勧めします。さらに、テーマに関してもチームメンバーに設定してもらってください、それによりチームメンバーのモチベーションを高めることができてカイゼン効果が期待できます。
「管理者・幹部からの支援」の要素
チーム・組織活動を活発にするためには、参加しているメンバーがお互いにコミュニケーションをとり、メンバーが自ら貢献しようとするモチベーションを持って、共通の目的を達成しようとすることが重要になります。管理者・幹部は、継続的にこれらのことを高め・結合していくための支援をする責任があります。管理者・幹部の支援が不十分であると、いくらメンバーが優秀であってもQCサークル活動は十分な成果を出せないばかりか、最悪の場合には活動が衰退します。
自作生産管理システム導入のメリット・デメリット
システムを導入して生産工程を見える化することで、在庫、納期、コストや工程などを適切に把握、管理することができるようになります。導入するシステムとして考えられるのは、広く市場に出回っている市販のシステム、いわゆるパッケージソフトと言われるものと、自社で開発する自作のシステムの大きく分けて2つになります。
前者と後者には長所、短所がありますので、どちらを選択するかは総合的に判断すれば良いかと思います。
ただし、中小企業の場合、情報システム部門がある、もしくは新事業としてシステム開発に取り組むなど以外では、自社開発は積極的にはお勧めいたしません。その理由は、自社で開発~運営までを行えば、自社の業務プロセスにマッチしたシステム導入ができますが、 開発、導入や運営・保守にかかる投入リソースに比べて、得るものがあまり多くないからです。
分類 | 長所 | 短所 |
自作システム | ・自社の生産工程、作業等にあったシステムを構築できる ・運営後も必要に応じて改造、変更をすることができる | ・リスクのある開発、導入と運営・保守などのコストを負担する必要がある ・システム担当者や部署を設置する必要がある ・担当者が退職した際に継続運営や更新が困難になりやすい ・直接的には利益を生まない業務にリソースを投入する必要がある |
市販システム | ・開発コスト費用負担が不要 ・導入、運営・保守、または更新に関してシステム専門家のサポートを受けることができる | ・自社の生産工程や作業をシステムに合わせる必要がある場合や、合致したシステムを導入できない可能性がある |
「自作すると導入コストを抑えることができるから」と言う方がいらっしゃいますが、それは間違いです。開発や導入時にかかる初期コストだけではなく、その後の運営・保守、さらには更新などの運転コストも必要であり、それらは非常にリスクの高いものになっています。
それでも、自作システム導入を選択する場合には、完全自社開発ではなく、しっかりしたシステムベンダーを参加させ、社長や幹部がプロジェクトリーダーとなったプロジェクトチームを構築してプロジェクト管理を行い、リスク低減のためにアジャイル型の開発手法などを導入することをお勧めします。
生産性が高い人の特徴と行動を解説!
生産性が高い人とはどのような特徴や行動特性をもっているのかについて、OECDで1位の労働生産性を誇る米国でのIT技術者のマインドや取り組み姿勢を参考に考えてみたいと思います。
「アーキテクチャの理解」
一流のITエンジニアと三流ITエンジニアで生産性に差が生じるのは、課題に取り掛かる際のアーキテクチャ理解度差に起因しています。例えば、目の前に問題が発生した場合や新たな技術が現れた際に、一流ITエンジニアは最初に自分の力だけでなく、周囲の力も借りてその問題の事実や技術の基礎をデータなどで分析します。問題や技術の構造(アーキテクチャ)を理解して、解決のための仮説づくりや技術の本質を見極めるために十分な時間をかけてから、実際に手を動かす、またはメンバーに指示を出します。
アーキテクチャと言うと難しいのですが、皆さんが楽しんでいるボードゲームでもアーキテクチャが重要です。具体的には、コンセプトやゲームを作った方の思い、ターゲット、ゲーム時間、登場人物やモノ、勝敗、ルール、展開などの骨格に相当するものです。このアーキテクチャを理解しているプレイヤーは、展開性、応用性、成長性、創造性において圧倒的な力を発揮することができます。
多くの日本の会社では、「まず自ら手を出して経験し、自ら理解して、その努力や挑戦を惜しまない」ことが善であり周囲からも評価されますが、それは時と場合によると考えておいた方がよさそうです。
「メンタルモデル」
メンタルモデルは元々認知心理学の用語で、人間が世界を理解し、意思決定を行い、問題を解決するために使用される枠組みや概念を示すもので、個々人やそれぞれの組織が過去の経験から無意識のうちに持っている、または意識的に作り上げた価値観を基にしたものあり、それぞれの人や組織の行動はそれにより決定づけるものと考えられています。
このような説明を聴くと、「メンタルモデルって難しすぎる」との声も聞こえてきそうですが、メンタルモデルは特別なことではありません、例えば皆さんも一度は名前を聞いたことのある、問題を発見した際に「なぜ」を5回繰り返すトヨタ自動車の「なぜなぜ分析」も、メンタルモデルに内包された理解を助ける手法を考えられています。メンタルモデルとは、個々人が物事を広範囲に捉える際に利用する「思考方法」や「思考の癖」と言ってよいかと思います。
トヨタ自動車は組織としてこのメンタルモデルがしっかりしているからこそ、全社的にカイゼン活動を通して高い生産性を発揮できるのだと考えられます。
「マインドセット」
皆さんは、職場などで「怠けている」とか、「手を抜きすぎている」と言われたらどう思いますか、多くの方は嫌な気持ちになることでしょう、しかし一流のITエンジニアは違っているようです。
彼らは最も優先順位の高い課題だけに取り組むようです。なぜなら、彼らが考えているのはどれだけ怠けて、手を抜いて成果を最大化するのか、つまり投入資源の最小化と創造価値の最大化に集中することだからです。このことを下式で考えてみると、日本人は分母にあたる時間など投入資源を流動的なものとして、分子の価値とのバランスをとって生産性を高めることを考えるのに対して、米国の一流ITエンジニアは分母を固定化・最小化として、分子の価値を最大化することで生産性を高めているとい言えるのではないかと思います。

働き方改革や少子高齢化による労働時間の短縮、若年層労働不足、シニア層や外国人などの新たな労働力の増加などの影響を受けやすい中小企業にとって、生産性を高めることは大企業にもまして取り組むべき大きな経営課題になっていくものと思われます。
\認定支援機関!補助金のプロの中小企業診断士がサポート/
工場の設備管理の重要性について解説
製造業において、生産設備の保全状態の良し悪しは直接的な生産性に直結していることから、非常に重要な課題です。どんなに良い生産設備やスキルの高い作業員がいても、生産設備が必要な時に所要の機能を発揮し続けられない状況では、高い生産性をもって良い品質の製品を安定して生産することはできません。
ところが、製造業の生産機械は長期使用される傾向にあり、15年以上使用されている割合は、金属工作機械の場合で約50%、鋼材・鋼板を加工する機械などの第二金属加工機械では約70%になっています。
そのため、すでに摩耗故障や経年劣化期間に入っているものが多くあるのだと思われます。これらは直接的に製品を生産するための生産機械に関することですが、間接的な設備であるユーティリティ設備も同じような傾向にあると考えられます。
長期使用機械・設備を安定的に稼働させるためには、質の高い・計画的な予防保守・整備を着実に行う必要があります。また、全員参加の生産保全の考え方から、設備を運転する作業員も、日ごろから「音」や「振動」、「匂い」などいつもとは違った現象見つけることが大事になります。
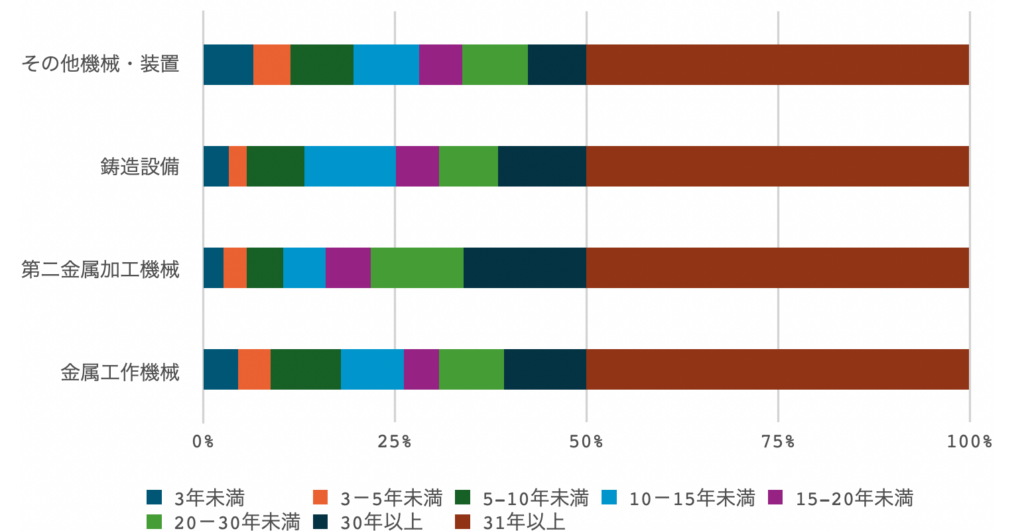
設備管理の業務は、生産していない休日や深夜の時間帯に行ったり、突然の故障対応など負荷が多かったり、安定稼働していることが当たり前と考えられることもあり、モチベーション高く取り組むことが難しく、従事する作業員を確保することが難しいところもあります。
しかし、多くの長期使用機械・設備がある中、少子高齢化への対応やDX・AI化などを進めるためには、従来にはないような新たな生産設備・機械も含めた設備導入を進めざるを得ません。今後作業員を確保して設備管理の質を向上することは、今までにも増して重要になっていくと考えます。
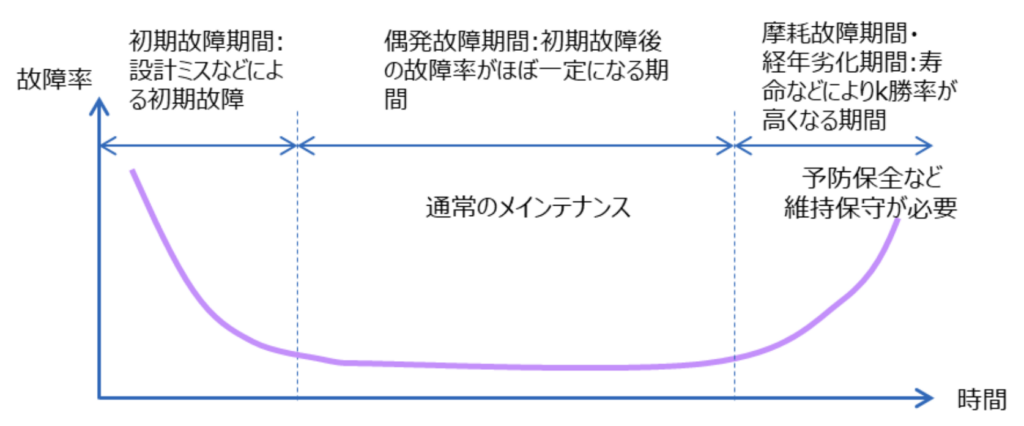
業務プロセス改善の目的と基本フローを解説
業務には、大きく分けて毎回決められた手順にそって作業を繰り返し進める業務と、毎回状況に応じて判断を行う必要がある業務の2つのタイプがあります。前者は「定型業務」と言い、例えば出張旅費の精算や給与計算などパターンのある業務、後者は「非定型業務」と言い、例えば顧客からの問い合わせなどの対外的折衝、新製品開発など思考して最適な解を導き出す創造的な業務が相当します。
一般的に、定型的な業務プロセスの改善は、プロセスの成果を担保しながらプロセス全体の投入リソースを最適化することになります。その場合の基本的な考え方は、ムリ、ムダ、ムラの見直し・削減を行うことになります。
一方、非定型的な業務プロセスの改善は、成果を最大化しながらも投入リソースを最適化する必要があります。その方法などについては別の機会に扱いたいと思います。
定型的な業務プロセスの改善においては、納期も含めた要求品質を満たす必要があります。効率を向上しようと一方的に投入リソースを削減することは本質的とは言えないため、実施する際には、これらのバランスをとりながら進めることが重要になります。
次に業務プロセス改善で期待できる効果について見ていきたいと思います。
「品質」
業務プロセス改善により作業や手順が標準化され、プロセス自体の品質が向上し、その結果成果品質も格段に向上します。また、プロセスの標準化や見える化によって、業務プロセスの属人化を解消することが可能となります。品質を担保して業務プロセスを担当することが可能になり、新人が入っても簡単に教育や引継ぎを行うことができます。さらに、業務プロセスや作業が標準化されていることから、業務プロセスの進捗確認やエビデンス対応、ITシステム導入による更なる改善を簡単に行うことができるようになります。
「コスト」
業務プロセスの改善では、それぞれの作業やプロセスを3Mの視点などで改善を行います。非効率な作業やプロセスの見直しが行われ、不必要な作業・プセスは排除・修正されて、コストの削減が期待できます。
「生産性」
付加価値である業務品質が向上して投入資源のコストを削減でき、生産性の向上を図ることが可能になります。また、改善活動を通じて、参加メンバーの一体感やモチベーションの向上が図れ、職場環境が良くなり、ワークライフバランスの向上が図れることでエンゲージメントの向上につながる、さらには顧客満足度の向上も期待できます。
基本的フロー | 注意点 |
あるべき姿を明確にする | あるべき姿(ゴール)と現状との差異を明確にして、それのギャップ(問題)を埋めるための改善を行うこととなるので、あるべき姿を具体的に明らかにします。 |
可視化、現状分析 | 業務プロセスに含まれる作業や業務を関係者にインタビューするなどして、関係部門ごとに整理して可視化し、関係者で現状を共有できるように整理します。 |
問題点洗い出し、優先順位付け | 可視化した業務プロセスから問題点を探して、優先順位付けを行います。 |
改善施策の検討 | 有効性と現実性の観点から問題の優先順位を決定したら、それぞれについて具体的な改善案を作成していきます。この時にすべての問題に対して行うのではく、上位の問題について取り組むようにします。 そして、「だれが、いつまでに、目標を達成するのか」を明確にしておくと、改善時、または改善後の評価で有用です。 |
改善施策の実践 | 先に決めた目標などとの比較を行いながらPDCAをまわして改善を進めていきます。 |
定着化と更なる改善 | 必要に応じて作業やプロセスの標準化を行うことで、定着化を図ります。 それと同時に新たな目標を設定するなど、次に改善活動につなげていきます。 |
業務プロセス改善にフレームワークとしてジャスト・イン・タイムを導入することで、ミスやトラブルを未然に防止でき、問題発生時の原因究明が早いと考える方もいるようです。しかし、ジャスト・イン・タイムの導入は、業務プロセスを整流化・平準化した後に導入することをお勧めします。整流化・平準化前に導入すると、業務の混乱に直面する可能性が非常に高いからです。
ECRSを用いた業務手順見直しによる効率化
生産現場において、作業改善を行う際に意識するとよいのがECRSの4原則になります。ECRSは、排除(Eliminate)、結合(Combine)、交換(Rearrange)、簡素化(Simplify)の英語の頭文字をとった略語です。これらは単独でも効果を発揮しますが、組み合わせることにより相乗効果を期待することができます。使用する場合には、排除(Eliminate)から順番に始めることを原則とします。
「排除(Eliminate)」
排除できないかについて考えます。見方を変えてみたり、少し視座を高くしてみたりすると、「なぜやっているのか、やめられるのではないか?」と思われる点が見つけやすくなります。この考え方は非常に効果があります。
ECRS全般に言えることですが、作業、原材料、道具、設備や工程の本当の目的を理解することが非常に大事になります。理解せずに排除を行った場合、その後に品質や生産性が悪くなる可能性もありますので注意が必要です。
「結合(Combine)」
結合できないかについて考えます。同じようなことをやっている場合は一緒にし、同時に進められる工程があれば統合することによって、大きな生産性の向上を期待することができます。
「交換(Rearrange)」
交換できないかについて考えます。仕事の手順を変えることはできないか、人や設備、道具類だけでなく、原材料や部品などを対象に変えることはできないかを考えるのです。入れ替えることや他のものと置き換えてみること、他の場所でやってみることなどを考えることで、改善の手がかりを探すことができます。
「簡素化(Simplify)」
単純化、簡素化できないかについて考えます。これによって作業の回数が減り、コストダウンに直結する改善を実現することができます。
5W1H | 検討の方向 |
Why(なぜ行う?) | やめることはできないか? |
When(いつ行うべき?) | 同時にできないか? 時間をずらす、入れ替えることはできないのか? |
Who(誰が行う?) | 他の人でできないのか? 同じ人でできないのか? |
Where(どこで行う?) | 場所を変えられないのか? 同じ場所でできないのか? その経路でないとダメなのか? |
What(何を行う?) | そのもの、作業でないとダメなのか? |
How(どのように行う?) | 他の方法はないのか? 簡単、短銃な方法はないのか? |
ECRSに関しては、改善案を検討する際によく使われる、以下に示す5W1Hの質問法も同時に使ってみると効果的に進めることができますので参考にしてみてください。
\認定支援機関!補助金のプロの中小企業診断士がサポート/
生産性の計算式を詳しく解説
昨年の11月日本生産性本部より、2022年度の日本の時間当たり名目労働生産性は5,110円、一人当たりの名目労働生産性は836万円と発表されました。前者は2019年から4年連続で上昇して1995年以降で最も高く、後者は2年連続で上昇してコロナ前のレベルまで回復しています。
これらの労働生産性は、分母を労働者数や労働総時間とし、分子を付加価値とする「付加価値労働生産性」と、分母を変えずに分子を生産量とした「物的労働生産性」があります。上記の名目労働生産性は「付加価値労働生産性」に分類されます。
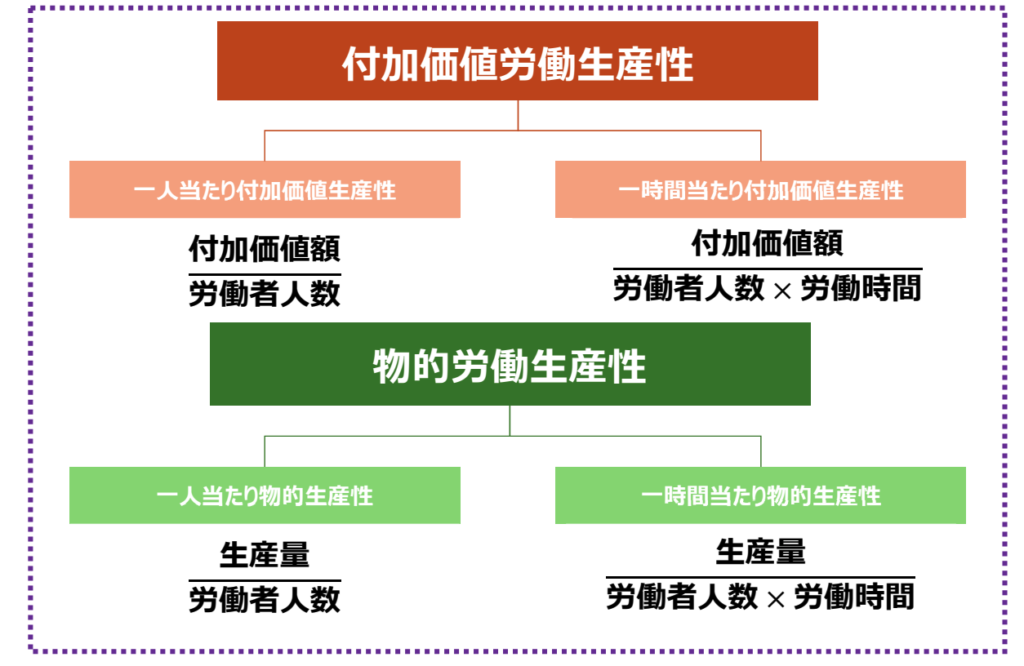
2022年度の日本の時間当たりの労働生産性が、4年連続で上昇した原因は何でしょうか?
設備等の有形資産の投入、それとも技術などの無形資産の増加によるものでしょうか?
この問いに答えるための指標として、マクロ経済学の考え方である全要素生産性(TFP)というものがあります。
総付加価値の増加率=
労働投入量の増加率+資本投入量の増加率+その他要素の増加率全要素生産性は以下の式で表されます。例えば、労働投入量が増えれば、その分だけ総生産量も増えるというわけです。なお、その他要素の増加によるものは、労働や資本投入要素の質向上や技術進歩、イノベーションなどによる寄与分となります。
総付加価値の増加率=
労働投⼊量の増加率+資本投⼊量の増加率+その他要素の増加率
この考え方を一般企業に拡張して当てはめると、以下の式で表すことができます。
付加価値(営業利益+⼈件費+賃借料+減価償却費+租税公課の増加率+知財収⼊)の増加率=
α×労働投⼊量増加率+(1-α)有形固定資産増加率+その他要素の増加率
α=(給与総額+福利厚⽣費)/付加価値額
ここで、日本の中小企業における付加価値向上率に与えるTFPの寄与率を見てみると、製造業においては労働や資本投入量による寄与度に比較してその他要素寄与度が高くなっています。
中小企業が付加価値を向上し続けるためには、設備投資だけでなく社員教育やモチベーション向上、カイゼン活動などのイノベーション等、貸借対照表に載らない無形資産に係わる施策を進める事が大事だと考えても良さそうです。
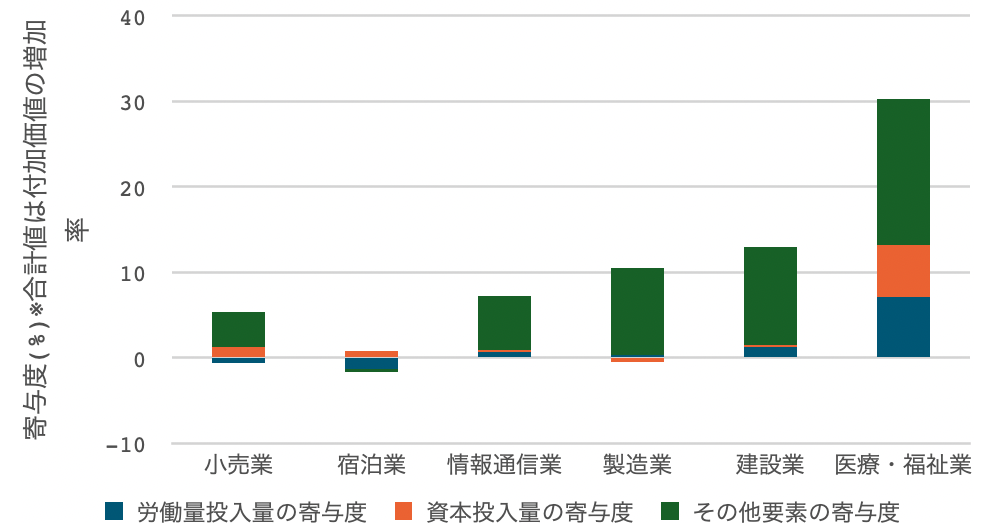
(2016年中小企業白書より筆者作成)
業務効率化によるシステム導入のポイント
業務効率化を図るためにシステム導入が必須だと考える方がいますが、システム化以外にもECRSの考え方を使って改善を図ることで実現可能です。自社の差別化や強みとは関係しない業務や付加価値が少ない業務などをアウトソーシングすることによって、業務の効率化を図ることも一例です。
しかし、システム化が業務効率化に有用であることも確かなことです。特に人の判断を必要としない定型的で付加価値の低い業務のシステム化は圧倒的な効率化が期待できますので、積極的にシステム化を検討すべきと考えます。
システム化は、業務削減や省力化による直接的な生産効率向上や品質向上、コスト削減につながるだけでなく、データによる業務管理やデータ分析による新たな価値創造も可能となります。効率化により余ったリソースを付加価値の高い業務へシフトすることで、さらなる価値創造も期待できます。
システム導入による業務効率化はメリットが多いのですが、いくつか留意しておくポイントがあります。
例えば、そもそもシステム導入の目的は何なのか?、どんな課題を解決するために導入するのか?、導入責任者・担当者はだれなのか?、導入後の保守はだれが担当するのか?などを事前に決めて、システム導入のリスクを低減しておく必要があります。それにより、システム導入時に発生する不具合に対する修正コストの発生リスクを低減することができます。
特に中小企業の場合は、社長、または幹部がプロジェクトリーダーとなってシステム化の各段階は関与し続けることが大前提です。そして、苦しみ悩みながらでも自分たちが中心で進めることをお勧めします。
パッケージソフトを導入する際、もし自社の業務フローに合わない場合は無理にソフト改造を行うのではなく、自社の業務フローを変更する方が標準作業化やシステム保守でのメリットが多い場合もあります。この点は是非事前によく検討しておくことをお勧めします。
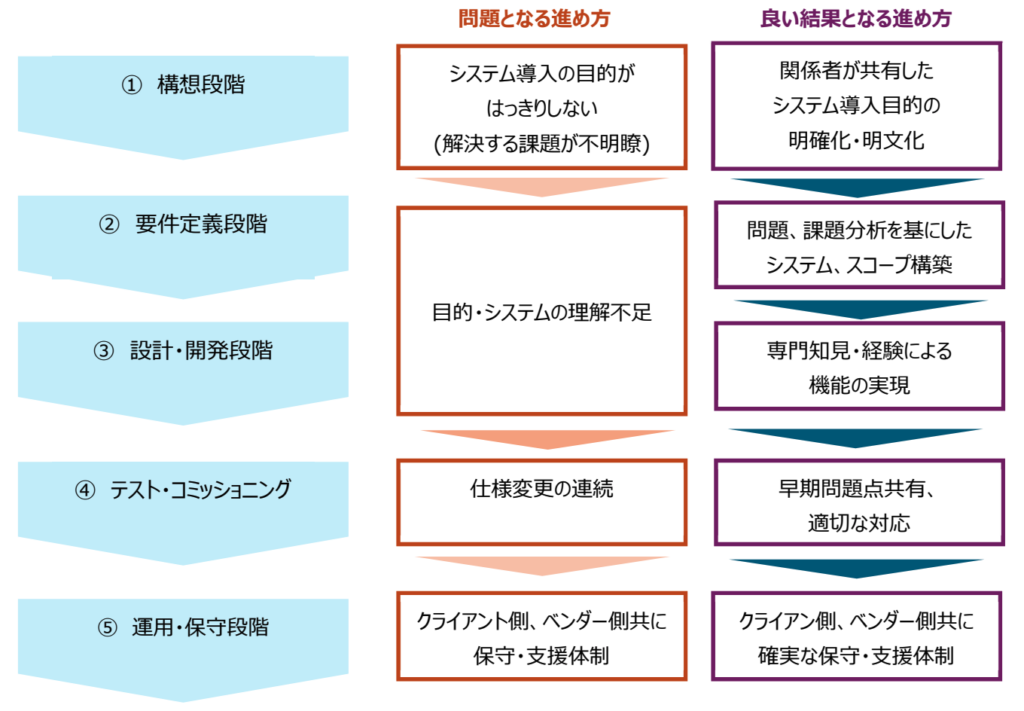
補助金の相談・支援は3Rマネジメントへ
当社は、中小企業支援に関する知識や経験があると国が認定した「認定経営革新等支援機関」に登録していますので、安心して補助金申請をお任せいただけます。
当社のサポート内容と依頼するメリットを以下にまとめましたので、支援先検討の参考になさってください。
\認定支援機関!補助金のプロの中小企業診断士がサポート/
3Rマネジメントのサポート内容
当社では、以下のとおりサポートを行っています。
・初回面談(オンライン)による相談受付
・申請書類の確認
・経営計画書などの申請書類の作成支援
・電子申請システムの入力支援
・採択後の交付申請支援
・交付決定後の遂行状況報告支援
・補助事業完了後の実績報告支援
当社では中小企業の事業再生に特化して支援をしてきましたので、補助金申請後においても、伴走型の経営改革・改善支援、融資や資金繰り、銀行対応等は特に強みが発揮できるところです。
3Rマネジメントへ相談・依頼するメリット
当社に相談・依頼するメリットを主に3つ紹介します。
・書類作成や申請の手間が減る
・採択決定後から実績報告まで支援がある
・採択される可能性が高くなる
補助金は、交付申請に多大な労力がかかりますので、当社では書類作成や電子申請システムの入力支援を行っていますので、手間が減り、本業に時間を費やすことができます。
また、採択されて補助事業実施後の実績報告においても相当な手間がかかります。そこで当社では、採択決定後の実績報告までの支援サービスを行っておりますので、安心してお任せいただけます。
なお、当社では、弁護士や税理士、社会保険労務士などの他仕業の方々や、製造業や飲食業、流通業などの会社員として実務を経験された中小企業診断士の専門家が多数在籍しています。
そのため、あらゆる業種の補助金申請においても、知見が備わっていることから高い採択率を保持できています。
\認定支援機関!補助金のプロの中小企業診断士がサポート/
まとめ
トヨタ式カイゼンについて解説しました。はじめから補助金ありきではなく、できることから実践することが重要です。
そのうえで、有益な補助金を活用することができる場合は、是非、申請をしていきましょう。
しかしながら、補助金は、申請するための準備や経営計画書など漏れなく書類を用意して、沢山の書類を書くため、多くの企業が専門家に支援を依頼して補助金の申請を行っています。
自社のみで採択されるためには、多くの時間と労力を割くことになりますし、競争相手も沢山いるため、採択は簡単なことではありません。
そのため、補助金の申請は、自社のみで行おうとせずに、専門家による申請代行や申請サポートを活用することをお勧めします。
当社3Rマネジメントでは、補助金の申請支援に注力しており、豊富なサポート実績や高い採択率を誇っております。
補助金の申請代行やサポートを活用したいと思われた際には、3Rマネジメントまでお気軽にご相談ください。
補助金に関する初回のご相談は、無料でお受けしています。
\認定支援機関!補助金のプロの中小企業診断士がサポート/